ABS is an impact, abrasive and thermally resistant, high quality thermoplastic material which is also ecologically sound with a high UV resistance.
Dollken’s surface printed ABS is sealed with a UV hardened acrylic varnish to give superb scratch resistance, as well as resistance to all standard domestic cleaning agents, meeting European standards DIN 68861, Part 1 and Part 2.
Modern kitchens are generally open plan and exposed to a variety of light sources. Dollken’s ABS meets the light fastness of wool scale 6-7, and will therefore not fade when exposed to the natural light normally found in a kitchen environment.
For the consumer it is definitely the heat resistance. ABS is thermally stable, whereas PVC shrinks when exposed to excessive heat around an oven, boiling kettle or toaster. This exposes the edges of the board substrate, allowing moisture to set in. Besides being unsightly, this will result in the substrate swelling and leading to possible de-lamination. For the kitchen manufacturer, it is easy processing. ABS is significantly lighter in weight and slightly softer than PVC, so the wear and tear on tooling is considerably reduced when using ABS.
Yes, ABS can be painted over without any priming or preparation. For painted doors, ABS edging give a good impact resistance under the painted edge. Dollken’s environmentally friendly ABS comes with an international ‘Green Guard’ certificate and has no chlorine compounds making this a totally biodegradable material.
For premium gloss panels and kitchen doors, a 1mm to 1.3mm is ideal – any thicker than that will reduce the effectiveness of the high gloss edge. The milled area will always be a matt finish so the smaller the milled area is, the better.
For conventional panels and kitchen doors, a 1.3mm or 1.5mm is most suitable. Both allow for a decent radius while reducing the ‘frame effect’ that a thicker edgebanding would produce. This is particularly noticeable on a woodgrain design, where the based colour is not identical to the surface print. 1.3mm and 1.5mm ABS edges are more flexible than 2mm and ideal for contour edgebanding.
For carcass edgebanding, a 1mm ABS is ideal. The ability to radius the edge will ensure no sharp edges.
For PVC wrap doors, you need high heat and moisture resistance PU dispersion with an integrated catalyst. For edgbanding, you need the highest heat resistant adhesive possible, with a low or zero filler content and extremely good adhesion properties.
For solid timber lamination, a high solid content D3 certified PVAC should be used.
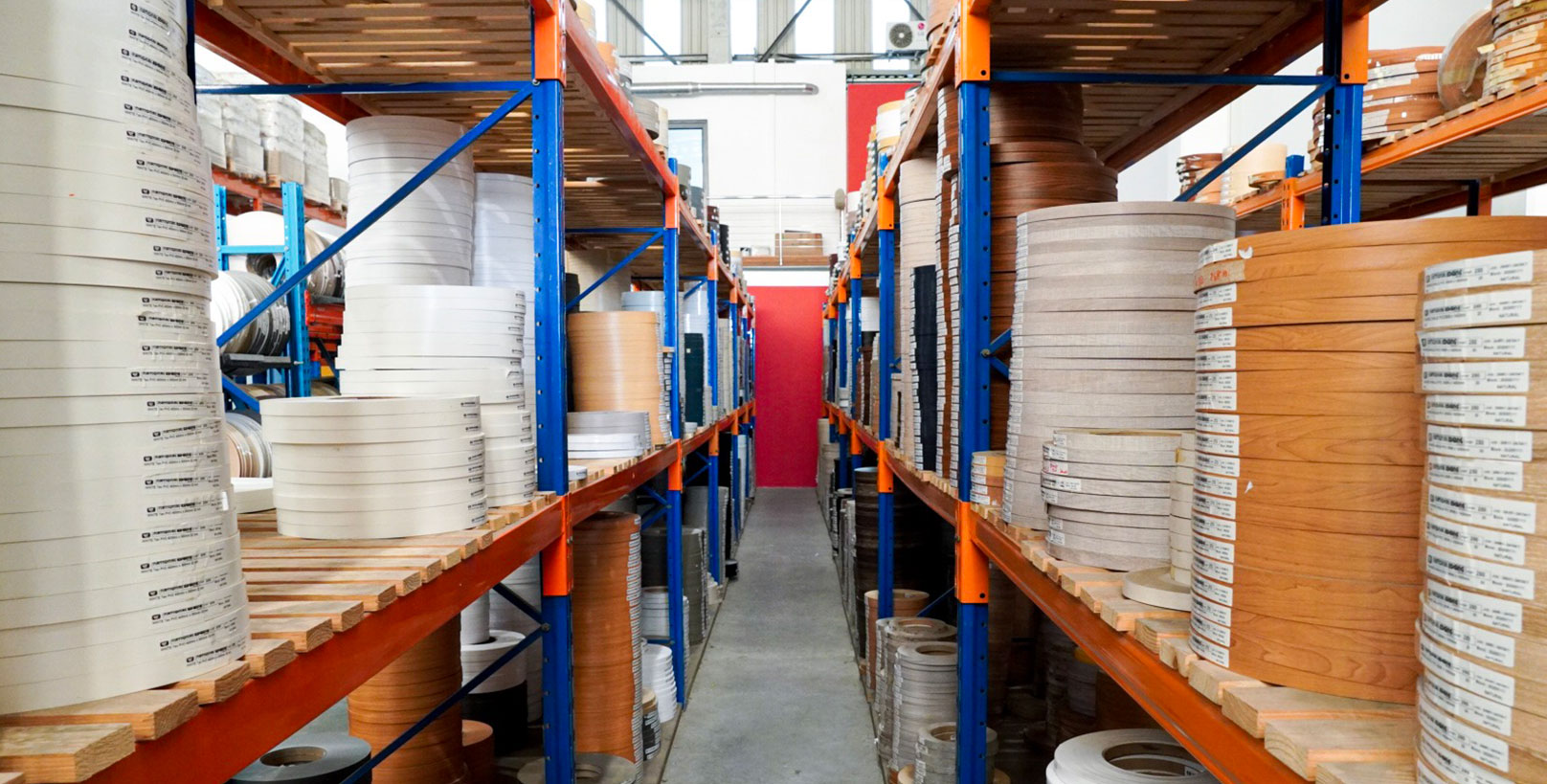